Why does pottery need to be dry before it goes into the kiln?
Clay that contains too much moisture can crack and even explode in the kiln. The heat causes the moisture in the clay to boil, causing it to expand and put pressure on the structural integrity of the pot. The dryer the clay, the less moisture it contains and the less chance you have of cracks.
Workable clay has a moisture content of about 20%. This water starts to evaporate – which means the clay is drying – as soon as it is in contact with the air. As a potter it’s not always easy to know whether your pot is ‘completely dry’. The layers of clay under the surface could still be damp, even when the outer layer feels dry. Your pot is only dry once the water has evaporated from those deeper layers as well.
Candling
The term ‘completely dry’ can be confusing. In actuality, even ‘completely dry’ pots still contain water molecules. Because the result of the drying process is that the clay will have the same amount of moisture as the air in the room. If you want to get rid of that last bit of moisture, you can dry out your pot in the kiln, at a low temperature, before you actually fire it. That’s called candling.
How do you know if the clay is completely dry?
The first rule is that you can’t trust your eyes. A piece may look dry, but that doesn’t mean it actually is. Luckily there are a few things you can do to determine how much moisture is still in the clay.
Temperature check
A temperature check is the fastest way to determine whether the clay is completely dry. Hold the pot agains your wrist or face and feel the temperature of the clay. Does it feel cold or cool at all? Then the clay has not dried out yet. Does the clay feel like it’s about room temperature, then it’s probably dry enough to go into the kiln. Are you not sure? Wait an extra day or two. Better safe than sorry!
Test tiles
Make a couple of test tiles from the same clay as your pot, with a similar thickness and size. If you think your pot is dry, break one of the test tiles and check the inner layers of clay. Do they look dry? Do they feel dry? Test tiles are a great way to determine how much moisture is left in the clay.

The drying process of clay
There is no golden rule that can tell you how long it takes before your clay is dry. Experienced potters have learned that there is quite a bit of variation in the amount of time it takes clay to dry. It depends on the thickness and size of the pot, the humidity in the workspace and the room temperature.
If you really want a rule of thumb, it’s best to expect about of week of drying time per half centimeter of clay. Don’t take unnecessary risks and check how dry the clay is with the temperature check or some test tiles. In the world of pottery it’s all about “practice makes perfect”. The more experience you have, the better you will be at estimating how dry your clay is.
Where can you find a kiln?
Just because you’re starting to learn pottery, doesn’t mean that you have to go out and buy a kiln. It’s not necessary. Most potters go to a studio in order to have their pieces fired. Once your work is ready to go into the kiln, it’s good to know that there are two types of kilns: frontloading and toploading. The difference between them doesn’t influence the firing schedule.
On this website you can find a helpful list of places where you can go to have your pottery fired. If you want to know how to transport your pots safely to the kiln, read this article.
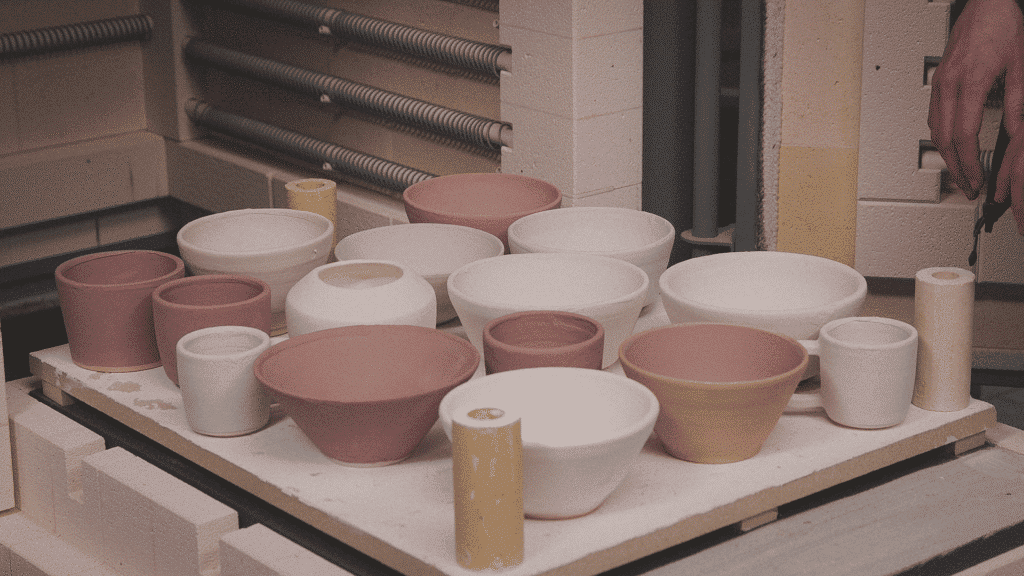
From clay to pottery
The transformation from clay to pottery happens in different stages. You can read about this transformation in this free overview of the different stages of clay. But here’s a quick summary:
1 Clay powder
Completely dry clay looks like powder. To be able to do anything with it, you add water.
2 Clay slip
If you add a lot of water to clay powder, you get clay slip. It can be used to glue different components of your project together, or to apply certain decoration techniques.
3 Plastic clay
Plastic clay is the easiest to work with. In this stage the clay feels cold and wet, and it’s ready to be sculpted, kneaded and thrown.
4 Leather-hard clay
Clay that has been drying for a while, is called leather-hard. If you bend clay in this stage, it will tear but not break. This is the perfect time to carve, smooth out, and add finishing touches.
5 Dry clay
Clay that is completely dry, has the same temperure and moisture content as its environment. In this moment, the clay is very fragile.
6 Bisque fired clay
A pot that is completely dry, can be fired. This first trip to the kiln is called abisque firing, and the clay is fired at a temperature of around 950°C. When it comes out of the kiln your pot will now have a lighter colour and it will have shrunk a bit. The main result of a bisque firing is that the clay becomes hard and permanent. In principle you can already call it ceramic.
But your work is not waterproof yet. For that you need to glaze it and fire it a second time. A bisque fired pot is perfect for glazing, because in this stage the clay will easily absorb the glaze.
7 Glaze fired clay
The second round of firing or glaze firing usually happens once you’ve applied glaze. It’s often at a temperature of about 1200 to 1300°C. After this firing the glazed clay will have glass-like look. Your work is now watertight, and when you tap it, you’ll hear a high-pitched sound.
Want to know in advance how much your pot will shrink in the kiln?
Then download the Cursist shrinkage ruler!
Firing clay in the kiln

The firing process takes about 8 to 10 hours. Followed by a cooldown period. The firing process happens very gradually. The temperature goes up very slowly. And the clay change bit by bit.
First the moisture that remains in the clay disappears and organic particles in the clay start to oxidise. When the temperature reaches 573°C, the quartz inversion happens. The quartz crystals in the clay rearrange, causing the clay to expand about 1% in volume.
If this step happens too fast, the clay will crack. That’s why it’s key to raise the temperature slowly! Around 750°C, the graphite and other carbon particles in the clay start to burn up. Once again, this step needs to happen slowly. If it goes too fast, the carbon will end up trapped inside the pot. And that result in the clay blackening and blistering.
Around 850 and 900°C, the clay starts to sinter: the silica particles in the clay melt and form a kind of glass layer. This makes the clay even more solid and waterproof. Another consequence is that you pot will shrink significantly. The sintering particles stick more closely together and fill the empty spaces created by organic particles burning up.
After both rounds of firing your pot needs to cool off. To be clear, your pot is now no longer clay. It’s officially become ceramic in the kiln.
Different types of clay, different firing temperatures
Clay is divided into three major categories, each of which requires a different firing temperature:
- Earthenware: between 800 and 1150°C;
- Stoneware: between 1150 and 1300°C;
- Porcelain: between 1200 and 1400°C.
You can usually find more information about the ideal firing temperature on the label of your clay.
Want to know more about clay?
Then download our beginner’s guide or take a running start with the beginner’s course From clay to pot.